An industrial valve or mechanical valve is a vital component for industrial applications made from usually metal alloys, ceramics, and various biocompatible plastics. It plays a crucial role in ensuring that industrial machines and systems run fluently and efficiently. The fluids or gases can be opened, closed, or partially obstructed passages in a piping system by using this device. It is available in different shapes, sizes, and materials based on their functions, designs, and applications for various purposes.
It is possible to regulate the flow of liquid or gas within a system by using the various types of Industrial valves. It has been used very much since the beginning of the 20th century. Nowadays, industrial valves are classified into 9 major types to suit different requirements. These cover all industrial applications and services. The choice of the perfect valve depends on several considerations.
Industrial Valve Definition
It is a special type of electro-mechanical component to regulate, control, or direct the flow of a fluid by opening, closing, or partially obstructing fluid flow within a system or process. Industrial or mechanical valves have the special ability to handle high pressure, either from fluids or gaseous materials. This effective mechanical component is built to control industrial processes. Industrial valves are very much used in a piping system that conveys liquids, gases, vapors, slurries, etc.
Industrial valve functions
There are many functions conducted by mechanical valves which are given below:
It is essential for starting or stopping the fluid flow.
It helps to control the direction of fluid flow within a piping system
It increases the safety of the piping system by relieving pressure or vacuum.
It regulates the flow of fluids within a piping system.
Industrial valve uses
Mechanical valve or industrial valve is mostly used in the industrial sectors for various industrial settings. It is used to control the flow of liquids and gases within large machinery. It can handle high pressure, either from fluid or gas and last through years of use in various systems or processes. Mechanical valves are essential components to control the fuel lines, boilers regulating steam pressure, air compressors, and adjust the airflow. It is also found to use water faucets, car engines, and HVAC systems nowadays.
Industrial valve types

Mechanical valves are designed in such a way that can be used for specific purposes easily. Their specialized designs and features meet the specific requirements of application fields. The nine major types of industrial valves with their features are explored below.
Ball valve
It consists of a ball to control and navigate the flow of fluids within a pipeline. It is used very much for controlling the flow and pressure in gas distribution systems and also for reducing the pressure connections with gas storage systems. This valve plays an important role in the food and oil processing industries. It can also be used in flowing systems on ships, fire-safe protection services, and chlorine manufacturing industries for fluid processing, transmission, and storage purposes.
Advantages of Ball valve
It is very easy to operate and can regulate the fluid flow within a second.
It has a compact and low-maintenance design.
It does not require the use of lubrication.
It has the poor throttling characteristics.
The design of this valve has flexibility and versatility.
Disadvantages of Ball Valve
This mechanical valve is not suitable for thicker media as sedimentation could occur and damage the valve disc & seat.
The surge pressure into this mechanical valve can create rapid closing and opening.
Ball Valve Applications
This valve is used very much for controlling corrosive fluids, slurries, normal liquids, and gases.
It is used in chemical and petrochemical industries, and even for residential uses.
Butterfly Valve
It is distinct from the other valves and consists of a concave disc that attaches to the valve stem. It is designed in such a way that it can control the fluid flow and limit the control capability. It is lightweight and creates a small install footprint.
Advantages of Butterfly Valve
This valve has a compact design and is lightweight.
It shows a minimal pressure drop.
This valve can be installed easily.
Disadvantages of Butterfly Valve
This valve has limited throttling capabilities.
The disc of this valve can be damaged when strong pressure is applied.
Butterfly Valve Applications
This valve is used to supply gas, supply of water, wastewater treatment, and fire protection purposes. It is also used in chemical and oil industries, in fuel handling systems, power generation, etc. It is very suitable for slurries, cryogenics, and vacuum services.
Check Valve
It is perfect for controlling the internal pressure, instead of outside action, for opening and closing purposes. It is also known as a non-return valve because it prevents backflow.
Advantages of check valve
It has a simple design and no need for human inspection for a long period of time.
This valve is very effective in preventing the backflow.
Check valves can also be used as a backup system in the industrial process.
Disadvantages of check valve
It is not suitable for throttling.
The dick of this valve gets stuck in the open position.
Applications of check valve
It is used in the pump and compressor to prevent the backflow. It is used in chemical and power plants for various reasons. Sugar refineries and the fertilizer industry use a check valve.
Gate Valve
It has a linear disc movement. The disc of this valve is either gate or wedge-shaped which has an effective shut-off and on mechanism. This valve is essential for isolation purposes.
Advantages of gate valve
A gate valve is used for bi-directional flow conditions.
It does not obstruct the flow when fully opened.
The design of the gate valve is very simple and very suitable for pipes with large diameters.
Disadvantages of gate valve
The throttlers are not good to control properly.
The gate or disc of this valve may be damaged for media flow intensity at the time of throttling purpose.
Applications of gate valve
The gate valve is suitable for water water treatment applications and neutral liquids. It is used for slurries and powder media. A straight-line flow of material without blocking is possible by using a gate valve.
Globe Valve
It looks like a globe with a plug-type disc. The throttling capabilities of this valve are very nice. The disc of this valve moves up unobstructedly to allow the flow of media. It is suitable for those fields that do not require high-pressure drops.
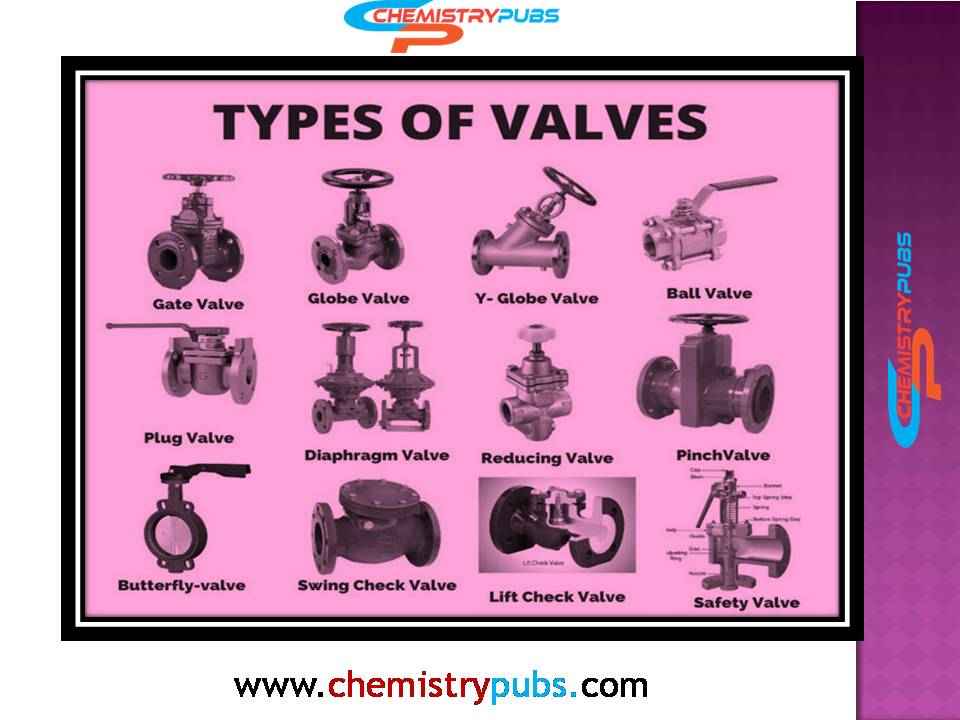
Advantages of globe valve
The shutting mechanism of the globe valve is better than other valves.
This valve can be repaired easily.
Disadvantages of globe valve
Globe valve is not perfect for high-pressure applications.
The high pressure damages the media flow path.
Applications of globe valve
The Globe valve is perfect for the regulation of the cooling water system. It can be used at high-point vents and low-point drains when the pressure drop is not a concern. Globe valve is perfect for running feedwater systems, chemical feed systems, extraction drain systems, and the like.
Needle Valve
The disc of this valve is like a needle. The mechanism of this valve is similar to that of the globe valve. It shows more precision and control in smaller piping systems.
Advantages of needle valve
It is very effective to control the fluid media.
It needs minimal mechanical force to seal the valve.
Disadvantages of needle valve
This valve requires quite a few turns to turn off and on completely.
This valve is only suitable for sophisticated shut-off applications.
Applications of needle valve
This valve controls the fluid flow and distribution purposes. It is associated with distribution points in pipe systems as a regulator of media. Needle valve can also be used in calibration applications.
Pinch Valve
Pinch valve is also called clamp valve used to stop/start and throttle. The linear motion of this valve allows unobstructed flow of media.
Advantages of pinch valve
The pinch valve has a simple design.
This valve does not contain any internal moving parts.
The pinch valve is perfect for slurries and thicker, even corrosive media.
It helps to prevent media contamination with a lower maintenance cost.
Disadvantages of pinch valve
The pinch valve is not suitable for high-pressure purposes.
This valve is not perfect for gaseous materials.
Applications of pinch valve
This valve is mostly used for unrestricted fluid flow. The various parts of this valve need complete isolation as well as environmental contaminants. It is perfect for chemical processing, and cement handling, among others.
Plug Valve
The disc of this valve acts as a bubble-tight shut-off and on plug or cylinder. The opening and closing mechanism of this valve is similar to that of the ball valve.
Advantages of plug valve
The mechanism of the plug valve is simple and easy to maintain.
The pressure drop of this valve is lower than the other valve.
This valve is reliable and has a tight seal capability.
It has fast action for closing and opening.
Disadvantages of plug valve
It requires an actuator to close or open the valve.
The plug valve is not ideal for throttling purposes.
It requires power or an automated actuator.
Applications of plug valve
The plug valve is perfect for controlling gas pipelines, slurries, and various applications that contain high levels of debris. This valve is ideal for running at high temperatures and pressure application purposes. A plug valve is an essential tool for controlling the highly abrasive and corrosive media.
Pressure Relief Valve
A pressure relief valve or pressure safety valve helps to release the pressure from the pipelines to maintain the pressure balance and avoid build-up. The main purpose of using this valve is to protect the equipment in an over-pressured event.
Advantages of the pressure relief valve
This valve is used for controlling all types of gas and liquid.
The pressure relief valve is ideal for high-pressure and temperature applications.
The pressure relief valve is cost-effective and needs less maintenance.
Disadvantages of pressure relief valve
The back pressure can create a harmful effect on running the valve mechanism.
Applications of pressure relief valve
This type of valve is suitable when back pressure is less required. It is used in boiler applications and pressure vessels.
Frequently Asked Questions (FAQs)
What is a mechanical valve or an industrial valve?
It is a mechanical piece of equipment used to regulate the flow of liquid or gas within a process or system that can be opened, closed, or partially obstructed in the path of fluids flow direction.
What are the functions of industrial valves?
An industrial valve is very important for starting or stopping the fluid flow. It needs to control the direction of fluid flow within a piping system.
What are the types of industrial valves?
There are nine types of industrial valves namely ball valve, butterfly valve, check valve, gate valve, globe valve, needle valve, pinch valve, plug valve, and pressure relief valve.
What are the uses of industrial valves?
Industrial valve is used to control the fluid flow in chemical industries, oil industries, fuel handling systems, power generation, etc. It is an essential piece of equipment to supply gas, supply of water, wastewater treatment, and fire protection purposes.
What are industrial valves made of?
Industrial valves are made from stainless steel, molybdenum, and/or even chromium alloys to control the fluids in pipelines, viscous fluid service, and cryogenic applications.
Why are industrial valves important?
They are essential pieces of equipment to regulate the fluids to keep pressure and temperature under control.